Changing Times in Global Trade
Over the last few decades, globalization has been the driving force behind the global economy, reshaping industries and creating interconnected markets across the world. At the heart of this global economic revolution was the rise of manufacturing in low-cost countries, where labor and resources were cheaper, allowing multinational corporations to scale production, reduce costs, and increase profits. However, recent trends suggest that the era of offshoring and global supply chains may be reaching its peak.
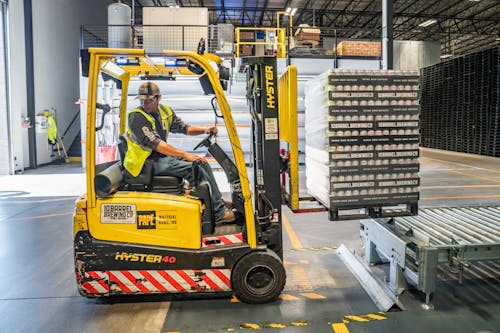
As global economies shift in response to changing technological, political, and social dynamics, many industries are beginning to reconsider the traditional model of outsourcing production. The rise of automation, regional trade agreements, shifting labor costs, and a renewed focus on national security have all contributed to a reevaluation of where and how goods are produced. This has led to what some are calling the “return of manufacturing,” with countries around the world moving towards reshoring operations that had once been offshored to distant regions.
Globalization and the Era of Offshoring
To understand why manufacturing is returning, it’s essential to look at the factors that propelled globalization in the first place. In the late 20th century, technological advances in logistics, communication, and transportation allowed companies to easily set up production in developing countries. China, India, and Southeast Asia became the epicenters of manufacturing for many global industries, from electronics to clothing, as companies sought to capitalize on cheap labor and minimal regulation.
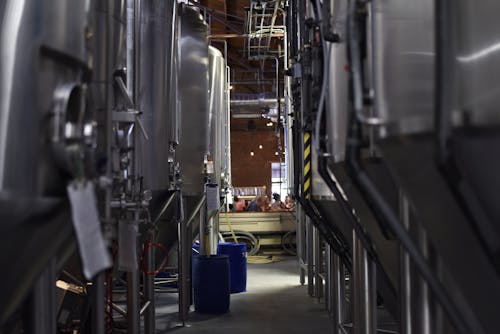
The strategy was highly effective in the short term. The labor force in countries like China was vast and inexpensive, and many of the global giants realized significant cost savings by relocating their factories. The ability to source raw materials cheaply, combined with low wages, enabled companies to produce goods at a fraction of the cost they would have in their home countries.
Moreover, the interconnectedness of global supply chains meant that raw materials and finished products could be traded and shipped across the world with minimal barriers. This led to economic booms in developing nations and gave rise to a consumer-driven global economy that reached into every corner of the world.
However, as the 21st century progressed, several factors began to alter this equation.
Why Manufacturing is Returning
- Rising Labor Costs in Traditional Manufacturing Hubs: One of the main drivers behind the shift away from offshoring is the rising cost of labor in countries that were once the main beneficiaries of globalization. In countries like China, wages have steadily increased as the economy has developed and the demand for skilled labor has grown. This has made it less advantageous for companies to rely on cheap labor from these regions, as the cost savings they once enjoyed are shrinking.
- The Impact of Technology and Automation: Technological advancements in automation and robotics have made it easier for companies to manufacture goods domestically, even when labor costs are higher. Automation allows for high-volume production at a lower cost per unit, reducing the need for a large workforce. As automation technology continues to improve, manufacturing processes become more efficient, and the need to outsource production to low-wage countries diminishes.
- Supply Chain Vulnerabilities: The COVID-19 pandemic has highlighted the vulnerabilities of global supply chains. With production facilities in distant countries facing shutdowns or delays, many industries found themselves unable to meet demand. The pandemic underscored the risks associated with relying on distant manufacturing hubs for critical supplies, prompting businesses to rethink their supply chain strategies. Many companies are now looking to shorten supply chains by reshoring production to regions closer to their consumer markets, allowing for more flexibility and resilience in the face of disruptions.
- Geopolitical Tensions and National Security Concerns: Increasing geopolitical tensions, particularly between the U.S. and China, have added another layer of complexity to global trade. National security concerns have led to a reevaluation of offshoring practices, especially in industries considered critical to national security, such as technology, pharmaceuticals, and defense. Countries are becoming more focused on ensuring that they have the capacity to produce essential goods domestically, in case global supply chains become strained or blocked.
- Environmental Considerations: The environmental costs associated with long-distance shipping and unsustainable production practices are also driving a reconsideration of manufacturing strategies. Transportation of goods across the globe contributes significantly to greenhouse gas emissions, and many countries are looking to reduce their carbon footprints by bringing manufacturing closer to home. Additionally, governments are increasingly incentivizing companies to adopt sustainable manufacturing practices, which often require greater oversight and regulation – something easier to manage locally than across distant borders.
- Consumer Preferences for Local Goods: Consumers today are more concerned with the origins of the products they buy. As interest in local, sustainable, and ethically produced goods rises, companies are responding by reshoring production. The “Made in [Country]” label has become a point of pride for many consumers, and manufacturers are finding that there is a market for locally produced goods, especially in regions with high disposable incomes.
The Challenges of Reshoring Manufacturing
While reshoring presents several benefits, it also comes with its own set of challenges. For many countries, especially those that have heavily relied on offshoring in the past, the infrastructure and workforce needed to support large-scale manufacturing simply may not be in place. Rebuilding the manufacturing sector often requires significant investment in technology, education, and facilities.
- High Initial Investment: Setting up domestic manufacturing operations requires a substantial upfront investment. Companies must invest in new equipment, facilities, and employee training to ensure that production can meet the standards required by consumers. The costs associated with reshoring can be prohibitive for smaller companies, even if long-term savings are achievable.
- Lack of Skilled Labor: Many advanced manufacturing sectors require specialized skills, and a shortage of skilled workers can present a barrier to reshoring efforts. Educational systems in many countries may not be fully prepared to train workers in the specific skills needed for modern manufacturing. Governments and industries will need to work together to address these gaps in the workforce.
- Rising Costs and Regulatory Hurdles: While labor costs are rising in traditional manufacturing hubs, labor in developed countries may still be more expensive than in developing countries. Additionally, stricter environmental regulations and labor laws in some regions can drive up production costs, making it difficult for companies to compete with low-cost alternatives from abroad.
- Global Supply Chain Complexity: Even if reshoring becomes more common, completely eliminating global supply chains is unlikely. Many industries still rely on parts and materials that are produced in other regions, and achieving true self-sufficiency would require a significant overhaul of global production and distribution networks. For many companies, balancing domestic production with international supply chains will be necessary to remain competitive.
Looking Ahead: The Future of Manufacturing and Globalization
As we look to the future, the global manufacturing landscape will likely be shaped by a combination of factors. While globalization is not likely to reverse entirely, its pace may slow as countries become more focused on strengthening domestic production capabilities.
Countries with strong industrial bases, like the U.S., Germany, and Japan, are already leading the way in reshoring efforts, especially in high-tech and automated industries. At the same time, emerging economies may continue to attract investment in industries that rely on lower-cost labor, though the nature of that investment may shift toward more sustainable and technologically advanced manufacturing practices.
In this evolving landscape, countries will need to adapt to remain competitive. Governments will play a crucial role in incentivizing reshoring through tax breaks, infrastructure investments, and educational initiatives that foster the skills necessary for modern manufacturing. Simultaneously, businesses will need to strike a balance between embracing the benefits of global trade and mitigating the risks associated with distant supply chains.
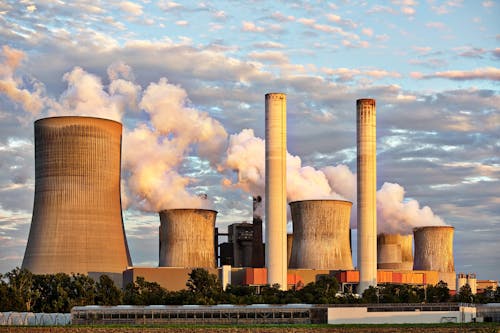
The return of manufacturing does not necessarily mean the end of globalization, but rather a shift in how and where production takes place. As the global economy continues to evolve, the interplay between local production and global trade will shape the future of industries and economies around the world.