The Rise of 3D Printing in Modern Manufacturing
In recent years, 3D printing has rapidly evolved from a niche technology to a transformative force in the world of manufacturing and innovation. Once limited to prototyping and small-scale production, 3D printing has now become a key tool in industries ranging from automotive to healthcare, aerospace, and consumer goods. This technology has the potential to revolutionize how products are designed, produced, and distributed, challenging traditional manufacturing processes and reshaping industries at their core.
At its core, 3D printing—also known as additive manufacturing—allows for the creation of three-dimensional objects by building up material layer by layer based on a digital model. Unlike traditional manufacturing techniques that involve cutting, molding, or assembling parts from larger raw materials, 3D printing offers a highly flexible and efficient alternative that enables more complex, customized, and on-demand production.
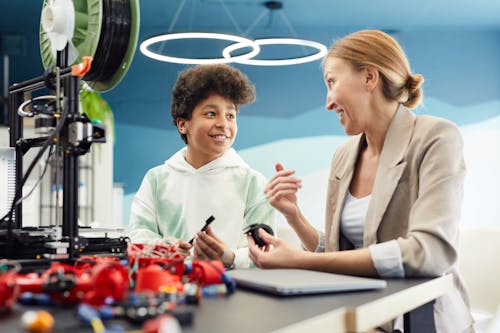
Streamlining the Production Process
One of the most significant impacts of 3D printing on manufacturing is its ability to streamline the production process. Traditional manufacturing methods often involve numerous stages, including design, prototyping, tooling, and assembly, each of which can be time-consuming and costly. 3D printing eliminates many of these steps, allowing for rapid prototyping and even full-scale production directly from digital designs.
This means that manufacturers can iterate on designs faster and more efficiently. The ability to rapidly produce prototypes allows engineers to test and refine concepts quickly, speeding up the product development cycle. Additionally, 3D printing reduces the need for expensive tooling and molds, which are typically required in traditional manufacturing. This is particularly advantageous for small-batch production or custom-made products, as it eliminates the high setup costs associated with traditional methods.
The flexibility of 3D printing also allows for greater design freedom. Engineers and designers are no longer constrained by the limitations of traditional manufacturing processes. Complex geometries that would be difficult or impossible to create using conventional methods can now be printed with relative ease. This has opened up new possibilities for creating products that are not only more functional but also lighter, stronger, and more efficient.
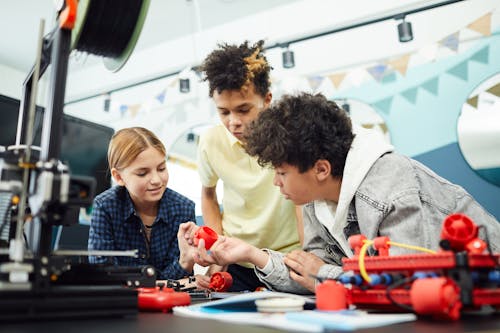
Customizability and Personalization
One of the most exciting aspects of 3D printing is its ability to produce highly customizable and personalized products. In industries such as healthcare, 3D printing has enabled the production of custom prosthetics, implants, and even dental devices tailored to the specific needs of individual patients. The ability to create bespoke products with a high degree of precision has the potential to transform patient care, making treatments more effective and improving the quality of life for patients.
Similarly, in the fashion and consumer goods sectors, 3D printing has made it possible to create personalized products that cater to individual preferences. From custom-fit footwear to personalized jewelry, 3D printing enables designers to offer consumers the ability to own products that are uniquely tailored to them. This level of personalization was previously unattainable with traditional manufacturing methods, which often rely on mass production techniques that result in standard, off-the-shelf products.
Reducing Waste and Promoting Sustainability
Another significant benefit of 3D printing is its potential to reduce waste and promote sustainability in manufacturing. Traditional manufacturing processes, particularly those that involve subtractive methods like milling or CNC machining, often generate significant waste material. The removal of excess material to create a finished product can result in a large amount of scrap, much of which ends up in landfills.
In contrast, 3D printing is an additive process, meaning that material is deposited only where it is needed. This drastically reduces the amount of waste produced during manufacturing. Additionally, 3D printing can use a variety of sustainable materials, including biodegradable plastics and recycled materials, further contributing to its environmental benefits.
In industries such as aerospace and automotive, 3D printing has also led to the development of lighter and more efficient components. By creating complex, lightweight structures that maintain strength and durability, manufacturers can reduce the overall weight of vehicles and aircraft, leading to energy savings and improved fuel efficiency. This focus on reducing material usage and optimizing designs for performance is driving greater sustainability across various industries.
Expanding the Reach of Innovation
3D printing is also democratizing innovation by making advanced manufacturing capabilities more accessible. In the past, small companies and startups often faced significant barriers to entry in the manufacturing world, such as high production costs, long lead times, and limited access to advanced machinery. With 3D printing, however, these barriers have been lowered, allowing small businesses and individual entrepreneurs to produce prototypes and small batches of products without the need for expensive equipment or infrastructure.
This has led to an explosion of creativity and innovation in various sectors. Startups can now bring their ideas to life quickly and affordably, while established companies can collaborate with external innovators to prototype new ideas and products in a fraction of the time it would take using traditional methods. As a result, 3D printing is helping to drive a more inclusive and diverse innovation ecosystem, where individuals and small businesses can compete alongside larger corporations.
Challenges and Limitations of 3D Printing
While 3D printing offers many advantages, there are still challenges and limitations to its widespread adoption. One of the biggest hurdles is the speed of production. While 3D printing is highly efficient for prototyping and small-batch production, it is not yet able to match the speed of traditional mass-production techniques for large-scale manufacturing. The layer-by-layer process of 3D printing can be time-consuming, particularly when producing large or complex parts.
Another limitation is the variety of materials available for 3D printing. While advances are being made in the development of new materials, the range of materials suitable for 3D printing is still more limited than what is available in traditional manufacturing. Certain materials, such as high-strength metals or composites, can be challenging to print with the necessary precision and durability for some applications.
Additionally, the cost of industrial-grade 3D printers and the specialized knowledge required to operate them can be prohibitively expensive for smaller businesses. While desktop 3D printers have become more affordable, large-scale manufacturing requires advanced systems that are still out of reach for many companies.
The Future of 3D Printing in Manufacturing
Despite these challenges, the future of 3D printing in manufacturing looks bright. As technology continues to improve, we can expect faster printing speeds, a wider range of printable materials, and better integration with other manufacturing processes. Hybrid systems that combine 3D printing with traditional manufacturing techniques are already being developed, allowing for the best of both worlds: the efficiency and scalability of traditional methods with the customization and flexibility of 3D printing.
Furthermore, as 3D printing becomes more widely adopted, new business models will emerge. Companies may move toward on-demand manufacturing, where products are printed as needed rather than produced in large quantities and stored in warehouses. This could reduce the need for inventory and lead to more localized production, reducing transportation costs and carbon footprints.
The potential applications of 3D printing are vast, and as the technology matures, its role in manufacturing and innovation will only continue to expand. From reshaping supply chains to enabling personalized products and more sustainable manufacturing processes, 3D printing is poised to change the way we think about production and innovation.

Conclusion
The impact of 3D printing on manufacturing and innovation cannot be overstated. This technology is transforming industries, enabling faster, more efficient production, and offering unprecedented opportunities for customization and personalization. As it continues to evolve, 3D printing has the potential to unlock new levels of creativity and sustainability while driving significant advancements in how products are made.
However, challenges remain in terms of speed, material limitations, and cost. As these obstacles are addressed, the full potential of 3D printing in manufacturing will become even more apparent, shaping the future of production and innovation in ways we are only beginning to imagine. Whether it’s creating complex components for aerospace or personalized medical devices, 3D printing is changing the way we create and think about products, marking the beginning of a new era in manufacturing.